Each controller type has its own Control Algorithm Menu. The explanation for each field is as follows:
14. Controller Tuning Parameters:
The controller tuning parameters that each controller may have. They allow you to make the controller work for a certain situation. For detailed information, refer to the topic of Controller Algorithm Description Section.
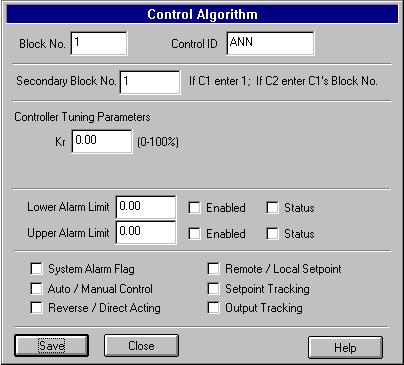
15.High Alarm Limit (HAL)
See Item 16 below.
16. Low Alarm Limit (LAL)
The high and low alarm limits for the measured variable. Use the enable field to enable/disable these alarms. The alarm status is shown on the Status area (not a filed).
17. System Alarm
The status flag for the system. If there is an error in the system such as the communication error, bad data error, etc, this flag is set.
18. Auto/Manual
Auto - set the loop to automatic control, or close the loop.
Manual - set the loop to manual control, or open the loop.
The flag to set the controller acting type:
Reverse - When the controller input increases, the controller output decreases.
Direct - When the controller input increases, the controller output increases and visa versa.
The reverse acting controllers are useful in applications. For instance, when the temperature in a reactor increases, you may want to close down the valve on the heating line. Be very cautious when using this option. If you set this option incorrectly, the controller will make the control action go in the wrong direction causing severe trouble or damage to the system.
20. Remote/Local
The flag to specify if the controller is given a Remote Setpoint or a Local Setpoint. This flag is used only if this block is a Secondary Controller. That is, its Block Number has been specified as the SBN in a Primary Controller.
Remote - it requests a remote setpoint from the Primary Block. In this mode, the setpoint cannot be changed manually.
Local - it leaves the setpoint to be selectable.
21. Setpoint Tracking (ST)
When the Setpoint Tracking flag is set to ON, the setpoint of the controller is forced to be equal to the measured variable just once and then resets by itself. This is useful for bumpless transfer.
22. Output tracking (OT)
When the Output Tracking flag is set to ON, it forces the controller to go to Manual and force OP = OTV. This is the safety feature that is very important for some loops. For instance, the value controlling the inflow that will cause the temperature of a reactor to go wild should be shut down in an emergency situation. The OTV should be configured to set the valve in a position for the shutdown. OT is the flag that triggers output tracking.