What is Neural Network?
In our human brain, there are millions and millions neurons that are connected in a certain way. We call it a neural network. [2]-[10]
When a brain is operating, the input messages going into the brain are processed through and stored in the neural network. Then, output messages are generated.]
For Processing: the new messages are compared with the existing messages, and then they are enhanced or attenuated, etc. (This is thinking and learning).]
For Storing: the messages are stored in the neural network. (This is memorizing).]
For Output: output messages are generated with thinking and learning processes to guide our activity and behavior. (This is guidance).
Example of How the Brain Works
When a child sees a long yellow object and is told it is a banana, he will remember it is a banana.
After he eats the banana, he will compare its taste with some other fruits he has had before. If he likes the taste and thinks it is better than an apple, he will remember that.
A few days later, when he sees a plate with bananas and apples, his brain will guide his hand to get a banana, not an apple.
What is ANN?
ANN -- Artificial Neural Network. ANN originated from the field of Bionics. ANN is actually a set of algorithms that can be implemented in a computer program to emulate the structure and information processing of neurons in the human brain.
Properties of ANN: parallel computation, self-learning, pattern-mapping, memory and associations, etc. In math, ANN can be represented by a set of nonlinear partial differential equations. Therefore, it could model strong nonlinear characteristics of a system.
The R & D of ANN started 15 years ago. It has been used in pattern recognition, image processing, and signal filtering.
A Popular Multi-Layered Analog ANN
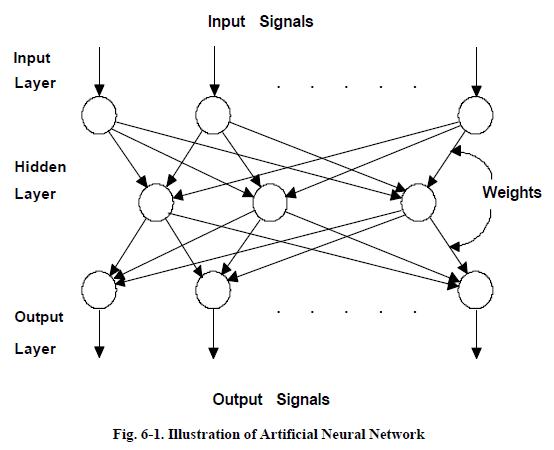
What is ANN Control?
In principle, both structure and parameters of an ANN can be upgraded based on some kind of algorithm to achieve control objectives. If we use an ANN block as a controller, the system becomes an adaptive control system.
We call: ANN based control methods -- ANN Control
What Contribution Has Western Thunder Made?
A new structure and algorithm of ANN has been invented. The new 1-For-3 controller can
- replace PID;
- control complex systems; and
- requires neither process model nor tuning.
Why Replace PID?
PID can control SISO process loops with satisfactory performance under these conditions:
- The process is linear and time-invariant and its dynamics can change only within a small range. (These conditions are too restrictive to many industrial processes),
- PID has to be tuned properly.
In practice, tuning the PID is often a frustrating experience if the loop number is large, the process response is slow, or the system perturbation drives the proper tuning away gradually. Due to these problems, many industrial loops today suffer from using PID, which causes problems in safety, quality, and productivity.
Is Self-Tuning PID Controller Better?
Yes. A well developed self-tuning PID control system can usually improve the situation, since the PID constants can be tuned on-line after the change of process dynamics.
However,
1) If the self-tuning is model based, it requires a bump in the process loop and it takes time to find the new process model in order to re-tune the PID. Process operators find this procedure uncomfortable.
2) If the self-tuning is rule based, the reliability of the tuning is sometimes questionable since it requires a complete knowledge of the process.
3) If a process is so complex that PID does not work, self-tuning would have no meaning.
How Does the 1-For-3 ANN Controller Work?
1) Based on the Model-Free Adaptive Control Theory, the 1 For 3 ANN Controller has the merits of being an Model-Free Adaptive Controller: No process model is needed, no controller design is required, and no complicated manual tuning of the controller parameter is required.
2) It is a highly adaptive controller that can compensate different process and environment uncertainties.
3) It does not require off-line training for the ANN. This has significant practical importance and is a big advantage compared to some other ANN control methods proposed in some research papers.
4) The self-learning algorithm is fast enough so that it can track the process dynamic change online.
5) The calculation time the ANN controller takes is quite short so that it can be implemented in many different platforms for real time control.
6) The number of ANN neurons is limited so that it does not require a special neuron network board to implement the controller.
7) It is designed to have only one tuning parameter, called ANN Response Knob, for the ANN controller so the operator can shape up the loop responses as he wishes.
Comparison of Startup and Tuning Procedure of PID and ANN
PID controller:
- Do an open-loop bump test to figure out the time constant, DC gain, and time delay of the process.
- Calculate PID constants based on these data and tune the PID with initial settings.
- Put controller in Auto.
- When the loop does not run well, re-tune the PID again and again.
ANN controller:
- Leave the ANN Response Knob to 50 percent as the default value.
- Put controller in Auto
- Shape up the loop by tuning the knob if necessary.
- The loop should run well with variations in system environment and process dynamics.
Besides Replacing PID, What Other Advantages Does ANN Have?
ANN control is able to deal with complex systems such as chemical reactors, blast furnace, distillation columns, and rolling mills.
These systems are usually nonlinear, their loops are coupled seriously, and the system dynamics have parameter and structure uncertainties.
ANN Properties for Controlling Complex Systems:
- ANN has powerful self-learning and adaptation capability to cope with uncertainties and variations in the system environment as well as the changes of control tasks.
- Control is only based on the closed-loop real-time input/output data and qualitative knowledge of the system behavior. No precise knowledge of system dynamics is required.
These are really big advantages of ANN control compared to other traditional control methods for complex systems.
How to Control a Complex System Traditionally?
Traditional advanced control techniques:
- Robust Control: Model Predictive Control: DMC,
- Adaptive Control: Model Reference and Self-tuning.
They depend on a precise and relatively simple dynamic model for the process. It is difficult to find such a model, and model uncertainties can affect the control performance seriously even if the model is obtained.
Due to the complexity of implementing these techniques, commercially practical control of complex industrial processes are very difficult and expensive. The 1-For-3 ANN control is a promising technology which can change this situation.
How is ANN Going to Affect the DCS, PLC, and Loop Controllers?
The 1-For-3 ANN controller works well for the personal computer based direct control system. The PC Control (PCC) system is getting more and more popular, especially the MS Windows NT operating system is very robust and well accepted by the process control industry.
In addition the technology is also a natural to be implemented in DCS, PLC, and single loop controllers. When this happens, the whole control product market will change.
When Did You Introduce the 1-For-3 ANN Controller?
Western Thunder introduced and demonstrated the first Artificial Neural Network based industrial controller at the ISA Show (Instrument Society of America) in October 1990. It was extremely well received and feedback was positive. ANN has now been introduced to a diverse and wide international market and continues to receive excellent reviews.
What Do You See for the Future of ANN Control?
Predictions are that the future of ANN control will be very bright.. We believe this technology will continue to improve and prove to be highly beneficial to present and future generations.