To resolve the problems caused by the identification mechanism, one simple and obvious solution is to eliminate the identification mechanism, or more generally speaking, the process model mechanism in the control scheme.
This is one of the main ideas defined in the Model-Free Adaptive Control. When an ANN controller is used as a MFAC controller, its system structure can be illustrated in Figure 3-1. When we adjust the weights of ANN as controller parameters, the ANN becomes an adaptive controller.
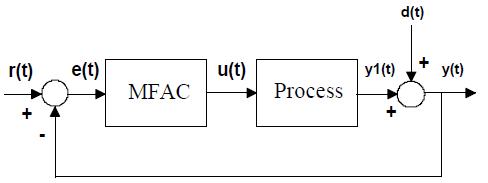
The signals shown in Fig. 2-1 are as follows:br/> r(t) -- Setpointbr/> y(t) -- Measured Variable or the Process Variablebr/> y1(t) - Process Outputbr/> u(t) -- Controller Outputbr/> d(t) -- Disturbance, the disturbance caused by noise or load changes.br/> e(t) -- Error between the Setpoint and Measured Variable.
The control objective is to make the measured variable y(t) track the given trajectory of its setpoint r(t) under variations of setpoint, disturbance, and process dynamics. In other words, the task of the ANN controller is to minimize the error e(t).
Notice that the system structure has been kept as simple as a PID system which makes the approach more valuable in real applications.
The ANN controller was designed to have only one tuning parameter, called the ANN Response Knob. An operator can use it to shape up the loop responses as he wishes. In other words, he can make the system response faster or slower with or without overshoot. The name 1-For-3 implies that one ANN tuning parameter replaces three PID parameters. [19][20]